Ecommerce
The Reorder Point Formula – How and When to Use it
- Written by Hayley Ward
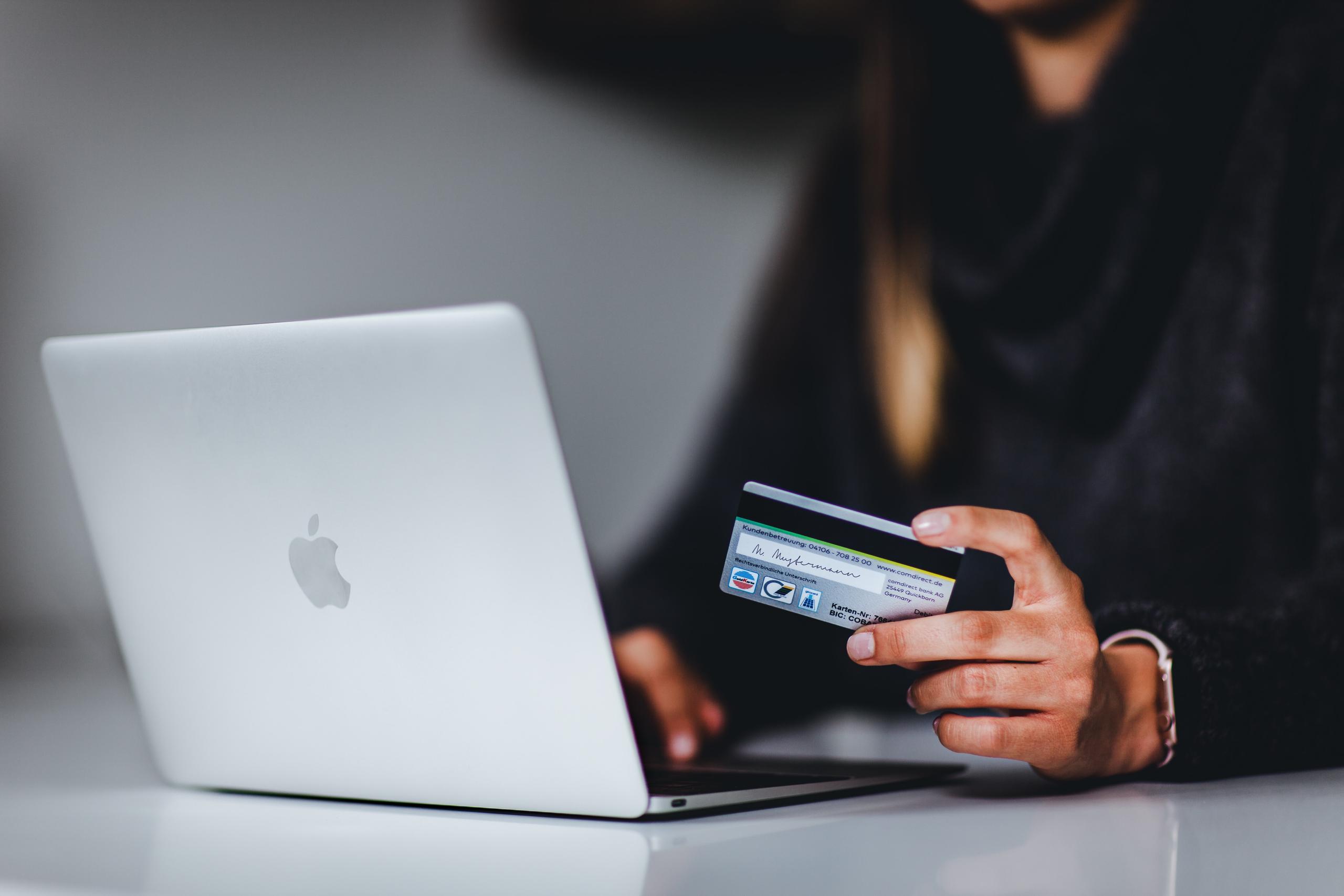
Overstocks account for 3.2 percent of lost revenue for the average retailer, while out-of-stocks account for 4.1 percent.
Reorder points can be a key tool for ecommerce businesses to ensure they always have the correct amount of stock on hand. This guide covers why to calculate and use reorder points.
With often thousands of product lines and SKU’s and ever-shortening delivery times expected from customers ensuring that product lines remain in stock is critical to retaining customers.
However, balancing this against the pressures of cash flow and storage challenges can be challenging and careful stock management measures need to be in place across all stock items. Applying reorder points to stock items is a relatively simple but effective method of ensuring stock is held at optimal levels.
What is a Reorder Point?
A reorder point is the point is the point at which you need to order more stock. It is used as a failsafe to ensure you won’t go out of stock for a specific product.
Why use reorder points?
Fundamentally, reorder points are used to give you greater control over your inventory. The advantages of this are:
Reduces the chances of stockouts
Stockouts not only lead to lost sales, they can also hurt credibility in your brand. If a customer tries to order from your store, only for the items they want to be unavailable, they will find another brand.
Helps reduce inventory costs
Using reorder points allows businesses to have less stock on hand (because they know when to order more and how long it will take). This makes it less likely that you will have unused inventory costing sitting in your warehouse costing you money.
What is the reorder point formula?
The ROP formula is relatively straightforward once you have the necessary figures to apply and can come in two forms:
- Average daily usage rate x Lead time
- (Average daily usage rate x Lead time) + Safety stock
Whereby:
- _Average daily usage rate_s = sales of that specific item each day
- Lead time = the length of time it takes to restock the item
- Safety stock = the amount of stock you as a business feel confident at holding for unforeseen circumstances. This may or may not be included in the formula and the difference between the two formulae are discussed below.
How & When to Calculate Reorder Points without Safety Stock
If you do not want to keep any safety stock a shortened version of the formula can be adopted:
Average daily usage rate x Lead time
Companies that operate ‘just in time’ or ‘Lean inventory management’ will often adopt this shortened formula. Other e-commerce businesses that stock a wide array of products may use this formula only on products that are not very popular and don’t sell very often but then use the additional safety stock calculation for their key lines.
As a rule, when you do not have a safety stock figure within the formula reorder frequencies tend to be higher.
This is best done over the course of a few months data so that variables in order values between days and seasons can be ironed out.
Let’s say you have a business that sells a range of gym and yoga clothing but the company is most well known for their trademark yoga pants. The data for sales over the past few months for yoga pants show:
So, the average daily usage rate is 3000 per month, so around 100 per day.
Lead Time: again, it is best practice to take an average over the same time period.
So, the average lead time for the yoga pants is 10 days.
So, for the yoga pants your readored point would be 1000 items (100 x 10).
As we said above, the basic formula for this is:
(Average daily usage rate x Lead time) + Safety stock
So the big questions then are:
- Should I set a safety stock level?
- If so, what should that level be?
When you should set a safety stock level
Any items that sell relatively slowly can have ROP calculated without a safety stock level as it does not matter too much if the product goes out of stock occasionally, or perhaps a nominal 1 unit can be added as a safety stock to trigger a reorder.
But when a stock item is key to a company’s success, such as a top-selling or fast-moving item, it is important to add a safety stock level.
It is important to note though that adding a safety stock figure for all stock across a wide range of products is likely to hike stock levels significantly and thus impact cash flow, and storage costs.
What’s the safety stock formula?
Safety stock = (max daily sales * max lead time in days) – (average daily sales * average lead time in days)
Let’s say you have a business that sells a range of gym and yoga clothing but the company is most well known for its trademark yoga pants. New designs of these come out each season to keep the range fresh. The company sells around 100 pairs of these per day but occasionally up to 200 pairs will sell.
It’s important to have enough stock to cover busy sales days but you do not want to be left with too many pairs at the end of the season when the new range is launched and the old style will have be sold at a discount. The yoga pants have a lead time of 10 days from the supplier but, on occasion, it has been up to 15 days.
Therefore:
Max daily sales = 200
Max lead time in days = 15
Average daily sales = 100
Average lead time in days= 10
Therefore the required safety stock level is:
Safety stock = (200 * 15) – (100 * 10) = 3000 – 1000 = 2000
So when the stock levels hit 2000 a reorder alert will be triggered.
Pros and cons of safety stock formula
So, albeit quite a simple formula the reorder point formulae can be utilised across a wide range of stock type and adapted not only to specific company needs but also to specific stock item characteristics.
When an item absolutely needs to be in stock constantly the use of the backup ‘safety stock’ amount is reassuring and, when calculated correctly, an effective stock control measurement. However, safety stock can add a cost burden to stock levels and this should be weighed up carefully against the need for safety stock.
Conversely, items that are extremely high value or not that critical to the reputation or profits of a business may not require the use of the ‘safety stock’ backstop, and Just in Time and Lean methods may work better.
It should also be noted that the reorder point only indicates at what stock levels to place an order; it does not calculate the number of items that should be ordered (which can be addressed by the economic order quantity formula).
If you want to have greater control over your inventory, then you should check out the advantages of using Veeqo’s inventory management software.